As one of the top suppliers of glass products in the country, the products of MG Company have been used for various famous constructions in Australia, such as Insulblind IGU with Integrated Blind for Hospital, Sky Glass for Balustrading in High Rise Apartments, Insulglass Select IGU for refurbishment of RMIT, St. Andrews House, and Residential Application, etc.
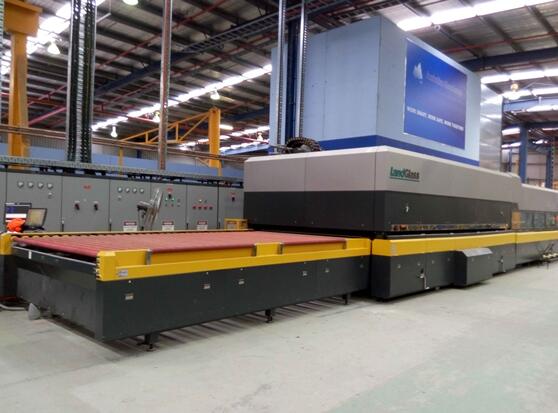
No doubt it’s a tough challenge. But working on-site toward a deadline was all too familiar to LandGlass’ crew. We have won this type of battle numerous times. The key to success lies in giving full consideration to on-site workload reduction throughout product design and manufacturing stages, well planning of on-site installation procedures, and close collaboration of field personnel. Having in mind the need to minimize the on-site installation work, the system adopted fully modularized design with components assembled in the factory whenever it’s possible. Installation procedures were detailed to each element with clear requirements on different types of responsible personnel and tools. Customer Service department also assigned skilled technicians who were familiar with local affairs to facilitate the communication. Before the arrival of the equipment, LandGlass had already sent experts in mechanical, electrical, and processing fields down to customer’s site. As soon as the equipment was unloaded, the crew was moving ahead quickly. It's not only a race against time and speed, it’s also a challenge to one’s physical strength and wisdom. In these 18 days, regardless of the 36℃ average ambient temperature and 10 hours a day work time, LandGlass’ crew worked hard and made no complaints. In close collaboration with MG’s staff, they successfully completed the installation and debugging within the time agreed.
When the time comes for equipment acceptance and trial production run, MG Company invited a senior expert from Sydney with many years of experience in glass processing industry and a well known reputation for his “zero tolerance” towards any product defect. Through good communication and cooperation between the parties, acceptance process was undertaken in an orderly fashion. The expert personally examined every piece of glass produced by LandGlass’ glass tempering furnace for its flatness, waviness, stress mark, and particle size, not letting go any defect.
After finishing the last step of the test, the expert could not hide his smile. He gave the general manger of MG a thumbs-up, “The product is extremely good!” At that moment, whether it’s the managers and staff members of MG or engineers from LandGlass, everyone at the scene burst into thunderous applause. It’s a battle won by dozens of dedicated people from both MG and LandGlass who worked around the clock!
When the acceptance test ended, the general manager of MG held the hand of LandGlass’ engineer and said, “As one of Australian up-scale glass products suppliers, we always want to provide to our customers high performance glass products. Our products have been widely used on many landmark buildings nationwide. I believe the high quality glass products made by this LandGlass glass tempering furnace will soon appear in various applications for many more new landmark buildings in Australia.”